車体に剛性を持たせる構造部材であるハニカム材の型紙を製作し、ハニカムをカットします。このハニカム材は曲面に対してもある程度自由度があり、プリプレグとの間に挟み込んで成形することで、軽量で高剛性を発揮します。ちなみにハニカムとは英語の「Honeycomb」で蜂の巣の意味。六角形を並べる形の構造のことです。
写真はハニカム材を使う部位に合わせての整えているところです。
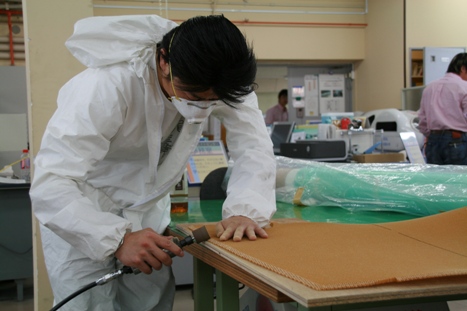
時期は6月に入ってすぐのあたりです。
Copyright 2007 大阪産業大学オキシライドプロジェクト
プリプレグを型に沿わせ、ハニカム材を接着フィルムによって固定していきます。プリプレグ→接着フィルム→ハニカム→接着フィルム→プリプレグの順で積層します。
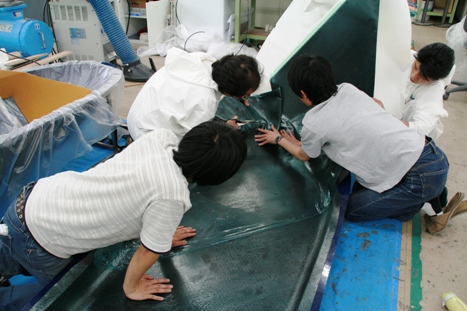
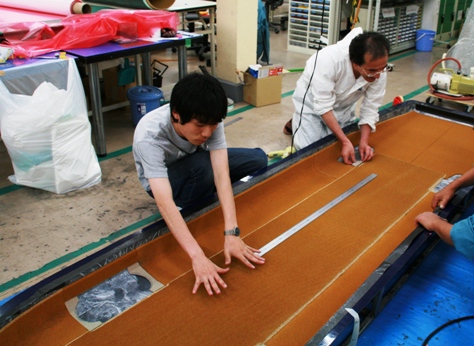
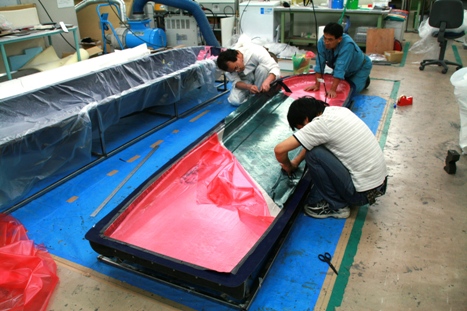
次にバックフィルムをシールテープで固定し、型を密閉します。そこに真空ポンプを使用して真空状態を作りカーボンクロスを型に密着させます。このとき、バックフィルムが引っ張れて破れないように凸凹の部分には余裕を持たせます。プリプレグが密着すると、型に縁板を乗せカウル合わせ面のシロの積層をし、また密着させます。
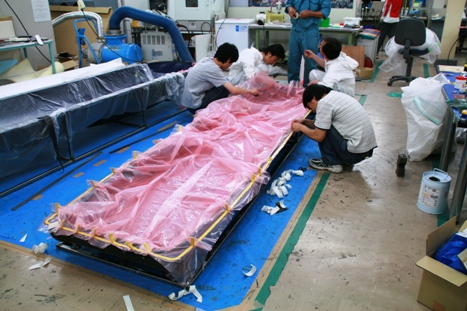
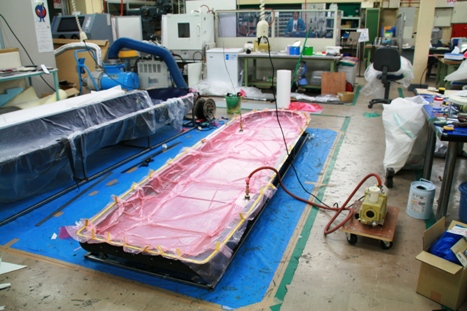
Copyright 2007 大阪産業大学オキシライドプロジェクト
オーブンにより加熱することで、プリプレグを硬化させボディを形作ります。このプリプレグは130度硬化のため、130度で約7時間置き硬化させます。その後、型から外しバリ取りなどを行い完成です。写真は、型の空焼の時にも登場したオーブンの外観です。
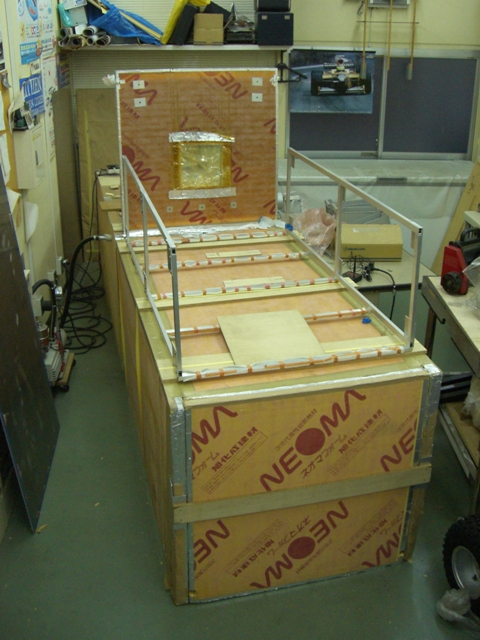
Copyright 2007 大阪産業大学オキシライドプロジェクト
アンダーカウルと同様にアッパーカウルも成形します。ただ、アッパーカウルはコクピットや窓の開口部、アクリル製のスクリーンを取り付ける縁などを設ける必要があるため、写真のように縁や分割線を考慮してプリプレグやハニカム材の貼り付けを行います。
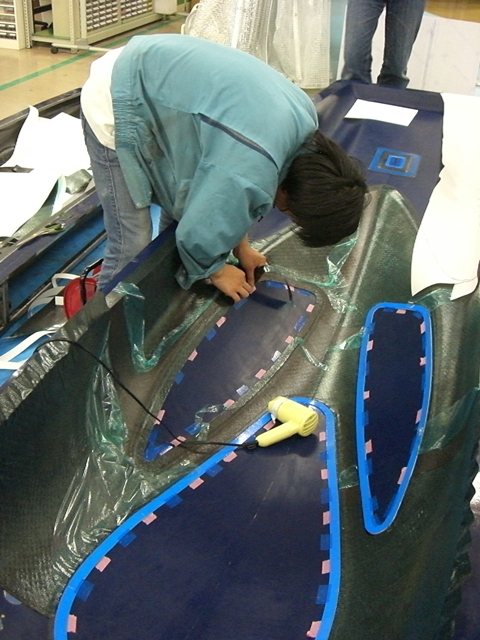
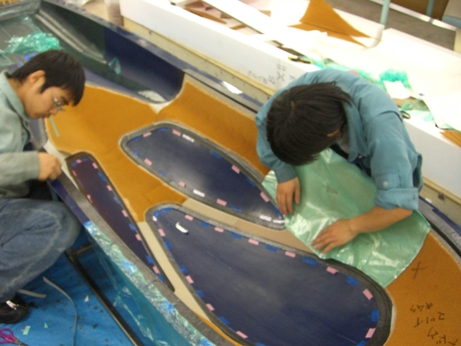
ここからは、アンダーカウルと同じく一度バック引きをしてプリプレグを密着させた後、縁板を使いカウルの合わせシロを積層してオーブンで硬化させます。
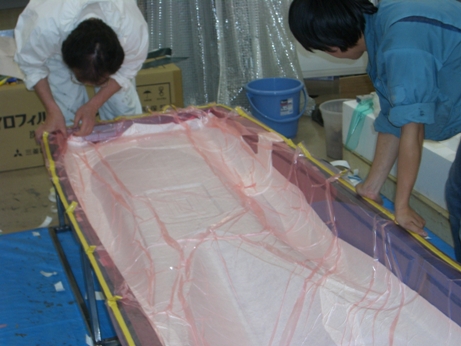
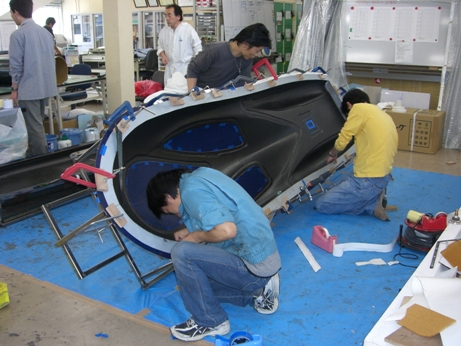
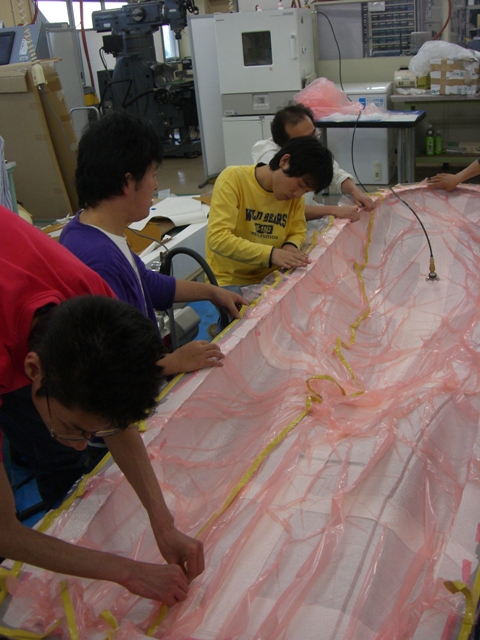
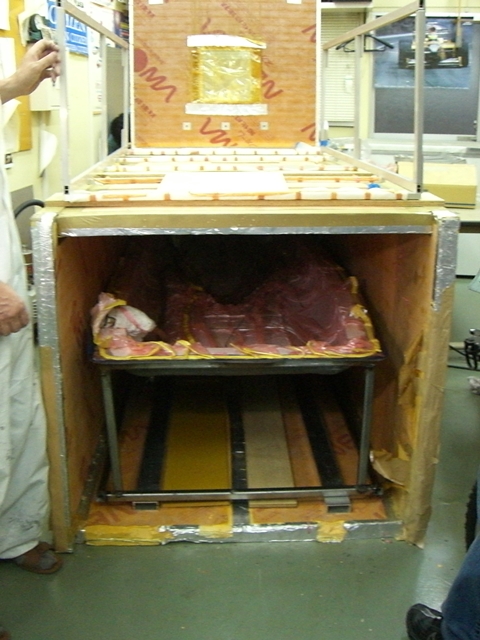
時期は6月10日前後でした。
Copyright 2007 大阪産業大学オキシライドプロジェクト
最近のコメント